News
ADVANCING GREEN LOGISTICS WITH INDETRUCK
The transportation industry is under increasing pressure to enhance sustainability while meeting the demands of performance, efficiency, and durability. In response, Indetruck, in collaboration with materials manufacturer Gurit and supply chain partner Gazechim Composites Ibérica, developed an innovative trailer flooring solution utilizing recycled-PET materials, with significant results.
Lightweighting to reduce emissions
As logistics moves toward decarbonization, the need for ecofriendly yet robust solutions is paramount. Traditional trailer floors made from wood contribute significantly to vehicle weight, increasing fuel consumption and emissions. Indetruck identified a gap for a lightweight, durable, and thermally-efficient trailer floor capable of withstanding the rigors of long-distance hauling.
The collaborative effort resulted in trailer floors composed of Gurit PET structural foam core, made from up to 100% recycled PET, replacing all wood components in the trailer floor, including the structural grid and plywood layers. Because of PET’s inherent thermal properties, the PU layer used as insulation in the original construction was also removed from the laminate.
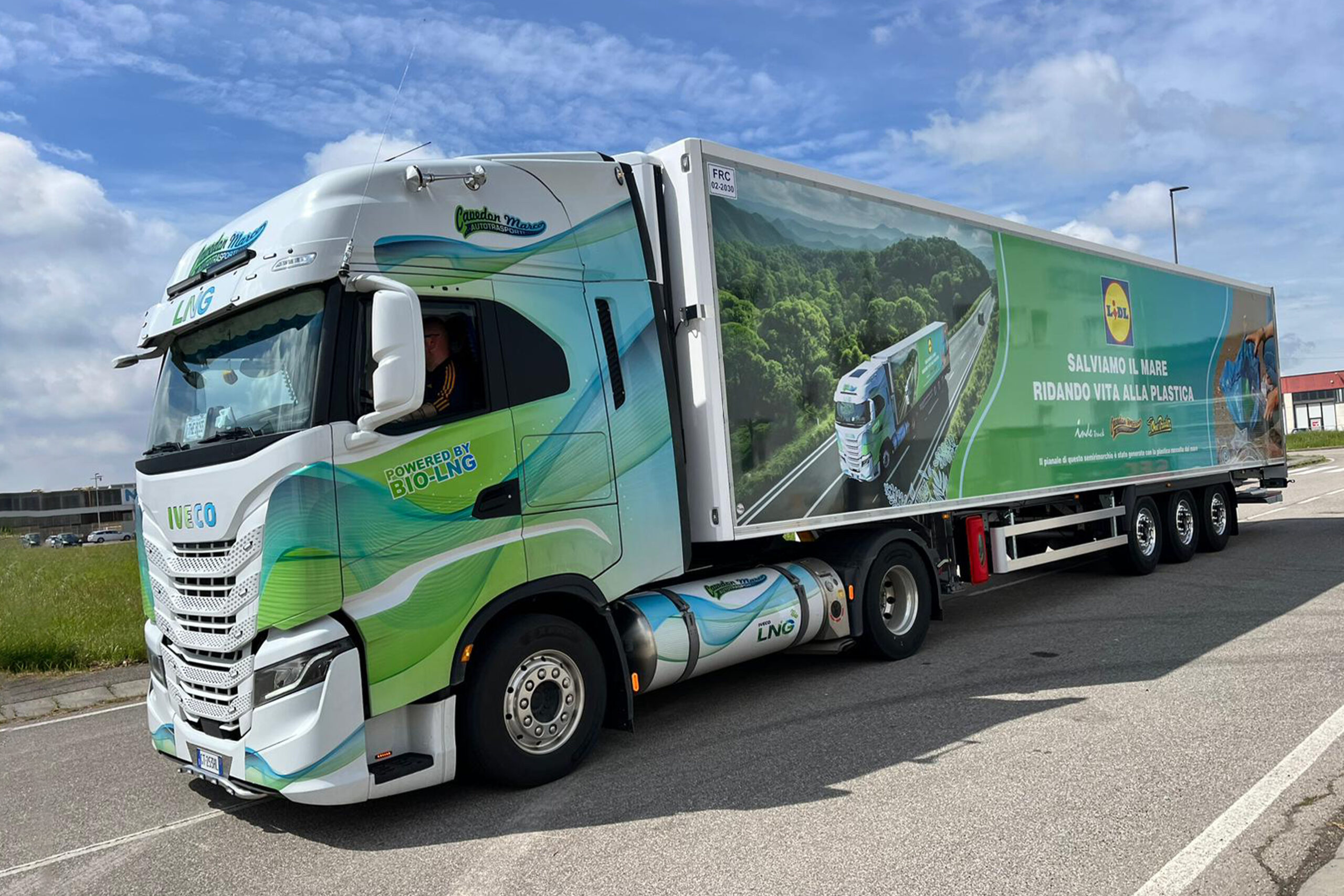
The complexity of the challenge
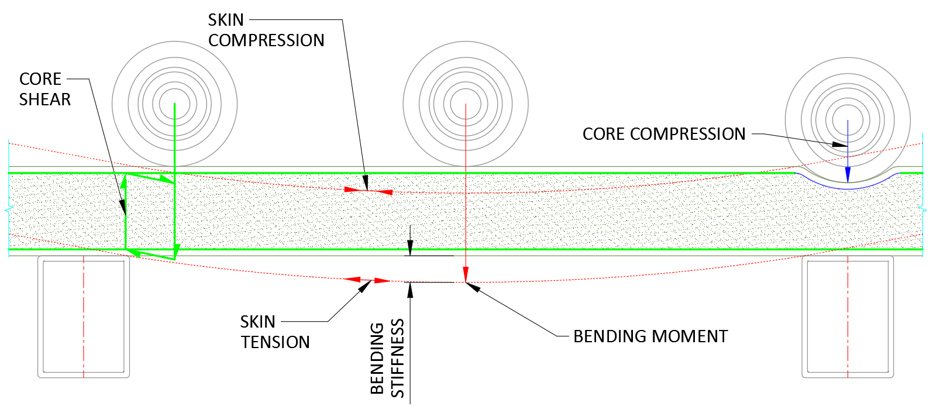
The original layup included plywood layers, a pinewood beam grid, PU insulation with frequent shear ties, and polyester laminated bonding layers. Gurit’s engineering team performed extensive structural analysis and testing to transition this incumbent laminate to a high-performing, lightweight PET solution compatible with existing manufacturing processes, and reducing costs by developing a panel with fewer constituent parts that would still address all needs.
Loads in several scenarios need to be considered when designing a trailer floor, which adds to the complexity. A trailer floor will experience a point load, when a pallet is first loaded onto the floor, via a wheel or series of small wheels on a trolley or forklift. A dynamic load is experienced when the forklift or trolley transitions from the load dock onto the trailer floor. And then there is the bending load as the cargo moves over the trailer floor. This is complicated by the fact the loading is unlikely to be uniform, as the trolley navigates the trailer floor crossing from mid panel to stiff supporting members of the chassis – and consequently, the load transfer to the steel chassis frame also needs to be considered.
Design and testing for optimization
Analysis was carried out on a simplified representative panel to develop an equivalent composite solution which had similar mechanical behavior under the specified payload. Using Finite Element Analysis, this was verified under the varying load scenarios and geometry, while simultaneously considering weight, insulation, and cost. Full-scale load tests using strip beams were carried out to compare current and proposed methods. The team estimated the cost of a floor panel that matched the strength and thermal performance of the existing design, proposing alternative floor to wall joint concepts to eliminate coach screws, assessing changes in material and labor costs and ensuring overall economic feasibility.
The new design proposed by Gurit’s engineering team simplified this trailer floor structure, using versatile Gurit PET for impact resistance, insulation, and structural performance, and reducing the need for shear ties. Thick glass fiber skins and a high density PET were used in the upper surface to deal with the point loads, distributing the load down and out into a layer of lower density PET. Higher density could have been used throughout but that would have compromised the weight, cost and insulation goals.
Gurit’s processing experts collaborated with Gazechim and Indetruck to ensure a smooth material transition, integrating optimized resin controls to lower weight further. To establish homologation and undergo thermal testing, Indetruck fabricated a prototype floor on-site, supported by Gazechim and Gurit; and later independently produced additional trailer floors with equally successful results.
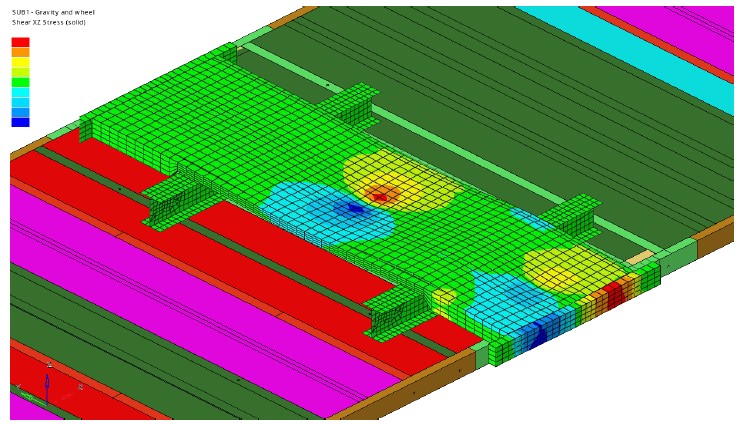
Positive sustainability impact
By using Gurit’s low weight PET structural foam core, Indetruck significantly reduces its carbon footprint during both truck manufacturing and in-service operation, thereby contributing to the decarbonization of the transportation sector. The PET used in the trailer floors are part of a sustainable and circular manufacturing approach. In every Indetruck trailer floor, approximately 15,000 post-consumer PET bottles are used, saving them from landfill and reducing carbon emissions. In addition, Gurit’s PET production waste is recycled back into the manufacturing process. By optimizing the material use and selecting lightweight structural materials, Indetruck is aligned with broader industry efforts to transition to zero-emission vehicles, as lighter trailer bodies are crucial for optimizing electric and hybrid truck performance and achieving the European Union’s mandate for a 45% reduction in CO2 emissions for new heavy trucks by 2030.
The trailer of the future
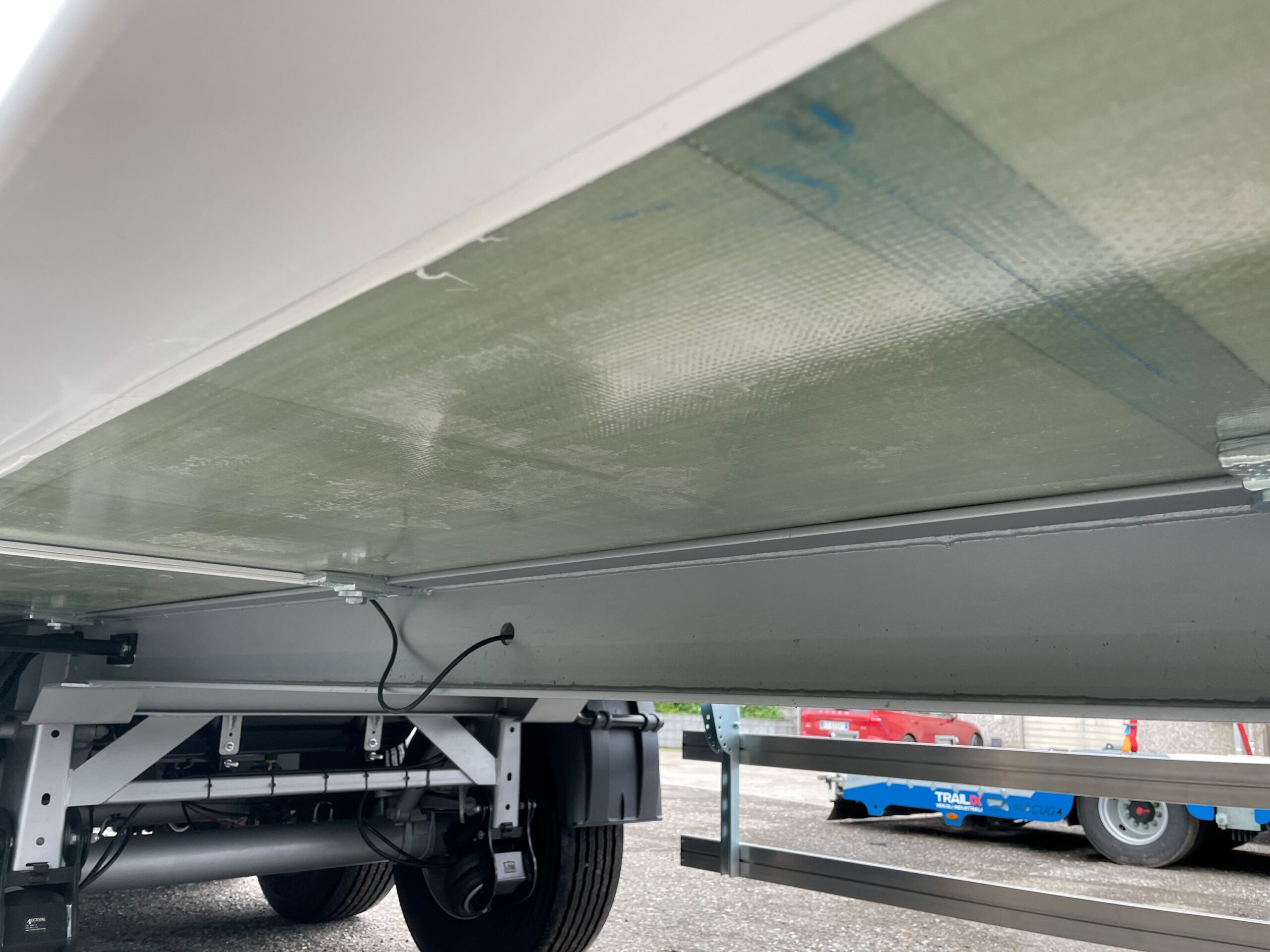
Energy-efficient and durable PET trailer floor
By using Gurit’s low weight PET structural foam core, Indetruck significantly reduces its carbon footprint during both truck manufacturing and in-service operation, thereby contributing to the decarbonization of the transportation sector. The PET used in the trailer floors are part of a sustainable and circular manufacturing approach. In every Indetruck trailer floor, approximately 15,000 post-consumer PET bottles are used, saving them from landfill and reducing carbon emissions. In addition, Gurit’s PET production waste is recycled back into the manufacturing process. By optimizing the material use and selecting lightweight structural materials, Indetruck is aligned with broader industry efforts to transition to zero-emission vehicles, as lighter trailer bodies are crucial for optimizing electric and hybrid truck performance and achieving the European Union’s mandate for a 45% reduction in CO2 emissions for new heavy trucks by 2030.